 |
The Step by Step Guide to Lean Business
By Oliver Wight Associate Les Brookes
LEAN! So much talk but just how much understanding
of how? There is clearly confusion between Lean, Agile, 6 Sigma, TQM,
etc. But what falls under the Lean umbrella and how do you get there?
And how do we avoid initiative overload? This article will run through
at strategic level how to approach Lean, and will also provide a proven
path approach to implementation that can be used across the whole of a
business, not just the manufacturing area which the term Lean Manufacturing
suggests.
 |
To most of us the term Lean would hopefully
suggest no fat or a minimum level of fat and applying this to business
would imply minimum levels of waste. Clearly this would then suggest that
to become lean we must remove that fat or waste from the business processes
to leave, wherever possible, just that activity that adds value to either
the external or internal customer. Whilst this would appear logical, actually
understanding that which is of value versus that which is not, and then
applying this to all aspects of a business is difficult. And often the
answers do not lie within the grasp of management running the business,
but with people who are actually closest to the process and hence better
placed to see the value and waste.
One of the key lean tools is that of “Value Stream Mapping”.
This tool when used correctly enables us to create a map of both value
and waste in a given process. This map can then be used to understand
the waste and its causes before moving on to remove it so that value flows
without interruption of waste. Clearly, whilst value stream mapping is
a key tool it is not just the tools of Lean which need to be understood
and used, but the implementation approach to adopt and the issues that
arise whilst implementing Lean. This article will discuss the Oliver Wight
unique approach, which broadly falls into five steps.
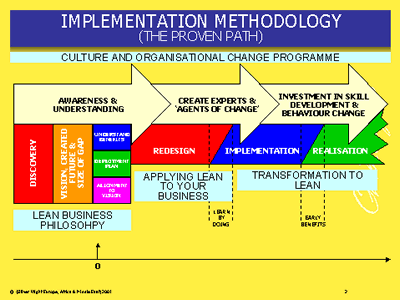 |
Step 1 - Lean Business
Philosophy.
Clearly, for the senior members of a business
to support any type of business improvement methodology or, for that matter,
change, there needs to be a vision of what the business would look like
after adoption and implementation of that philosophy.
For Lean this is no different, and one of the first pitfalls to be avoided
is jumping onto the Lean bandwagon through fear of being left behind.
First, the senior board must grasp what is meant by Lean, where are the
opportunities, where are the dangers, what level of commitment will be
required, how should the management of the business support the implementation,
and finally what the benefits will be.
This first step needs to take senior members and key decision makers through
the above issues in some detail so that they gain a good understanding
of how to create Lean. It is preferable for them to gain this understanding
by visiting Lean through an action-based learning simulation to give them
first hand experience of the key issues. The purpose of this first step
is to a) decide whether Lean is an approach that can be supported by them
and the business, b) to define a vision of lean for the business, c) to
create an implementation plan, d) to decide on the key sponsor, e) to
ensure that Lean will deliver the businesses strategic objectives, f)
to fully understand the management and culture change that needs to take
place in order to deliver a truly Lean business, g) to assign a budget
and analyse the benefits and h) to create a top level value stream map
of the business.
Then prioritise the implementation, which is of major importance as it
is often assumed that the biggest area for improvement is in the manufacturing/processing
areas. Actually, the opposite can be true as most businesses have been
focused on manufacturing for some years and may well find to improve support
parts of the process actually unlock more potential in manufacturing as
a result. Clearly, the vision and plans then need to be communicated to
the workforce.
Step 2 - Culture and
Organisational change programme
As with all philosophies which require business
change in order to implement we have to take great care of our most important
assets - people. Lean is certainly no different but has as big an impact
on management as it does on the workforce, but in completely different
ways. In step 1 senior management will have gained an understanding of
the impact that Lean can have on people, culture and the changes that
will be required. With Lean, the people who can most easily get to grips
with value-adding and non-value adding activities are the workforce. It
is for this reason that for Lean to work we need to adopt a bottom- up
approach which is led and supported by a visionary senior group and facilitated
by middle management. The main reason for this is that waste is far easier
to understand and remove as close to where it is created in the process
i.e. by the process operators. Therefore, in order to make this approach
work we need to consider the ability of the process operators to work
in process related teams, rather than their current functional ones, because
to develop Lean correctly requires teams to become truly self directed,
allowing problems to pick the people required to solve them from within
the teams rather than management to pick the problems.
In conjunction, middle management need to adopt a different approach which
is clearly heavily biased towards facilitation and being the key motivators
to help create the passion and relentlessness required in the pursuit
of Lean. There are a couple of other key changes for middle management
to contend with. The first of these is the inevitable move away from strong
functional ownership to ownership of the process. This is essential if
we are to unlock the waste which is a function of the process or which
has been caused by the functional boundaries existing.
The second change is one of understanding and behaviour which relates
to the way that over years management has focused their improvement activity
around the value-adding areas in the process, along with the people in
it. These people are sometimes seen as being responsible for the waste
when the reality is that the value-add often represents between 1% and
5% of the total process. This approach has led to a poor culture between
the workforce and management with the workforce tending to be wary of
change due to feeling victims of it.
With this stage it is essential to have a co-ordinated people and teams
programme which runs alongside the lean activity and education to ensure
that all members of staff are correctly coached. This avoids conflict
and delivers a management group that can facilitate change with the teams
working for them and so remove waste efficiently. The people and change
programme can be co-ordinated by the HR director at the senior levels
but as much as possible be part of the deliverable learning activity of
Lean. This is to ensure that education can be followed directly by application
to the work environment.
Step 3 - Applying
Lean to Your Business
This stage whilst not as involved from a
time point of view is clearly an essential factor in success It involves
educating middle management and the change agents in the Lean business
philosophy, create understanding of how this can be applied and re-focus
them to move from a hands-on improvement role of management to a facilitation
role. At this stage we begin to deal with the cultural and behavioural
issues that can exist between the management and workforce, and also with
management releasing some of the ownership of improvement to put belief
into the Lean process as a way of driving the business forward. The other
key issue for this group is that Lean will cut across functional/departmental
boundaries which will eventually lead to a restructuring of responsibility
for the major business processes rather than the current functional ownership
of a departments activity.
Step 4 - Transformation to Lean
The transformation process can now begin.
We will have set up a steering group, created a vision, selected and trained
change agents along with middle management, agreed an implementation path,
defined the core business processes and identified the process owners,
which may have taken away some of the traditional functional responsibility.
We are now ready to move onto application. Application involves five critical
steps as can be seen in the diagram below. This will be covered in detail
in a later article, so that for now we can focus on the higher level issues
surrounding this stage, which are People, Education, Support and Approach.
 |
We need at this point to form teams of about
12 people, some of whom will come from the process to be used for the
initial education and training, with the minority (2) coming from outside
of the process to act as third party objective team members. The Oliver
Wight Approach is to run an action-based learning event to both educate
the team in Lean and its application to a process. This is achieved by
facilitating the team in creating value stream maps of the current process
prior to goal setting and the team creating a new Lean process, along
with an implementation plan and budget. It is important that the education
given at this stage is that which can be directly applied and then, when
the team is ready to move forward to the next level of detail, further
education in the form of additional tools is given, again on the basis
of application as part of the process. We find that this approach is essential
as education without application is so often a waste for all. Support
at this stage will come in the form of middle management facilitation
to ensure that the team is able to deliver on time against their implementation
plan. The key here is not to take ownership of the plan but to provide
conditions in which the team can implement. The aim of this approach is
to create a nucleus of people who are trained in the Lean tools and techniques,
who have experienced Lean through hands-on application and who can then
with some external support move on to help others create lean processes
by transferring their knowledge.
Step 5 - Sustainability.
Sustainability is often one of the problems
with any business philosophy adopted. Often this comes about as a result
of lack of senior commitment, no goal alignment throughout the organisation,
lack of understanding and no alignment to strategy. This is why step 1
is of great importance to both cover these issues and also to ensure that
management understand that Lean is not just another initiative. The words
relentless and passion have been used earlier in this article. These words
suggest ongoing, commitment, desire and pursuit, which are all long term
and can only be achieved through behavioural and cultural change to a
business where waste is not acceptable to anyone.
The other important aspect of sustainability is to have a system for both
result- based and process based performance measurement including measures
for velocity of the overall business process and the individual business
processes.
The performance monitoring should then be encompassed within the Sales
and Operations planning Process, which should be being used to drive all
aspects of the business at the senior group level.
In conclusion, Lean can deliver huge benefits to any business, whether
in manufacturing, service, repair or government sectors, by following
a Proven Path Approach which will be broken down into more detail in future
articles Success can be achieved providing that the commitment is there
at senior level and that companies recognise the need for some external
support.
Prior to joining Oliver
Wight as an Associate Les was Head of Operations for Ilmor Engineering
Ltd who design and manufacture the Mercedes Benz Formula engines.
He implemented MRPII whilst simultaneously working across the business
on implementing lean manufacturing. Les's background is one where
high performance in operations is a must that adds to the competitive
advantage seen in the product. |
top of page |
 |