 |
Delivering Benchmark Levels of Business Excellence
through TPM
By Peter Willmott WCS International Ltd.
Introduction
Increasing pressure to drive down costs and eliminate waste in all its
forms across the Value/Supply Chain means the Continuous Improvement of
our Assets – both physical and people related – is no longer
an option that can be avoided.
The problem is that becoming world class is as much about buy-in to common
goals as market and technology driven opportunities. This requires building
the right management environment and shopfloor culture over time.
The question is - How can we assess the benefits, map our progress and
guide the journey?
The EFQM Excellence Model™
or Business Excellence Model (BEM)
provides a Toolkit for carrying out a very structured organisational health
check. As such, the BEM provides the essential checks and balances. The
company-wide approach to TPM provides a clear, practical, coherent, “enabling
tool” to continuously improve a company’s “score”
on the BEM and also the means to compare and benchmark with others.
30 years ago, Total Productive Maintenance showed the world that it is
a very practical route to higher levels of equipment effectiveness. Since
then, experience has shown that equipment and process problems are the
root cause of many of the unplanned events that reinforce a reactive management
style. Delivering reliable equipment on its own however, is not enough
to deliver world class company performance. TPM has therefore evolved
to address these wider management issues.
The company-wide approach to TPM in the sense of Total Productive Manufacturing,
provides a clear, practical, coherent, “enabling tool” to
continuously improve a company’s business efficiency and performance.
Together, the BEM and the TPM delivery process can give British Industry
in terms of both large and Small Medium Enterprises, additional means
for gaining and then sustaining competitive advantage.
This guide sets out the framework for using both tools together, in order
to release the productive potential of process equipment and people through
the elimination of waste in all its forms. Examples of using the BEM criteria
are an essential part of the guide.
These notes are relevant to all of us - whether managers or advisors -
who are involved in the elimination of waste in order to maximise added
value across the supply chain.
How can we Benchmark and Share TPM Best Practice?
The EFQM Excellence Model ™
or Business Excellence Model (BEM)
provides a Toolkit for carrying out a very structured organisational health
check. As such the BEM provides checks and balances for (tactically) managing
and (strategically) developing a business. The company-wide approach to
TPM provides a clear, practical, coherent, “enabling tool”
to continuously improve a company’s “score” on the BEM
and also the means to compare and benchmark with others.
This guide draws together the practical, transparent and coherent links
that exist between the widely accepted BEM toolkit and the TPM delivery
process, in order to give British Industry additional means for competitive
advantage via Best Practice TPM and Benchmarking.
EFQM & BEM
EFQM - European
Foundation for Quality Management was established in September
1988.
EFQM Mission is: -
• |
To stimulate and assist organisations throughout Europe
to participate in improvement activities leading ultimately to excellence
in customer satisfaction, employee satisfaction, impact on society
and business results; and |
• |
To support the managers of European organisations in
accelerating the process of making Total Quality Management a decisive
factor for achieving global competitive advantage. |
In the UK, the EFQM is represented by its partner organisation,
The British
Quality Foundation.
BEM - Because the BEM encourages the
identification and sharing of best practices it is a powerful tool for
performance improvement. In the UK, the EFQM Excellence Model™ is
also referred to as the Business Excellence Model (BEM). At the heart
of the BEM is the principle that the BEM is a self assessment tool. It
consists of the 9 criteria shown below that provide a framework for exploring
the link between organisational activities (or “enablers”)
and results.
 |
The
BEM Benchmark
The Business Excellence Model provides an independent and widely accepted
benchmark for managing the balance between strategic intent and tactical
application across the business. It considers five enablers (Leadership,
Policy + Strategy, People,
Partnership + Resources
and Processes) and four
results (Customer, People,
Society and Key
Performance). It measures how closely the bottom up, day-to-day reality
in each of the nine criteria reflects the intent set out in the top-down
strategic vision and direction.
Through a scoring framework, organisations track their improvement progress
by self-assessment, as well as comparing their own performance against
rigorous independent benchmarks set by successful companies. This helps
identify areas for improvement and priorities for action.
TPM & BEM
Through TPM all personnel are involved in continuous improvement activities,
providing the opportunity to set and reinforce a common set of values
and behaviours: on the shop floor TPM is driven by basic, hands-on goals,
such as zero breakdowns and practical enabling tools to deliver it and
much more.
Top down TPM is driven by a single business agenda supported by a structured
management process proven to raise equipment output, customer service,
reduced costs and improved safety, morale and of course, quality. It is
an holistic approach releasing hidden value in current and future operations.
TPM works by helping management to systematically identify and then reduce
hidden losses. This requires the level of attention to detail that is
only possible by involving those who carry out the work.
TPM is an obvious quality tool to deploy in a manufacturing organisation
of any size. It is primarily concerned with creating an environment in
which individuals and teams are most likely to use all their productive
resources in the most effective way. In turn this will lead to improved
results, particularly in manufacturing effectiveness, but also in terms
of health and safety, environmental concerns, customer and employee satisfaction,
as well as hard financial returns: All key components of the BEM.
The TPM audit and coaching framework sets out a clear
route map to zero breakdowns, waste elimination and beyond. As such it
provides:
• |
An objective assessment of the progress
and level of policy deployment |
• |
Coaching to guide further progress at Shop Floor
Team as well as First Line and Senior Management levels |
• |
Feedback from the value adding processes
to guide management decision making and prioritisation. |
The outputs from the TPM audit coaching process can
then be interpreted using the Business Excellence Model - to provide a
realistic Standard and Benchmark of progress in order to focus future
direction and action.
TPM and other Management Tools
TPM does not replace, nor does it conflict with, other management approaches
such as Just in Time, lean production or ISO 9000. In fact, it compliments
and supports them. In helping to reduce waste, TPM has a beneficial effect
on environmental issues. In essence, BEM affects everything your company
does - directly and indirectly. TPM can help you to do them all better.
What is TPM?
You have probably restructured your manufacturing operation in order to
bring down labour costs and refocused the company around its core activities.
You may have introduced Just-in-Time to reduce stocks and sought to build
a Total Quality Culture. What else can you do to improve your competitiveness?
Total Productive Maintenance (TPM) or, if you prefer, Total Productive
Manufacturing, can slash unit costs in manufacturing and process industries
by ensuring that plant and equipment are used to their maximum effectiveness.
In the last few years, a number of large companies have implemented TPM.
For many, the process has been hugely successful. Many more companies,
including small, medium enterprises (SME’s) are realising that adopting
TPM Principles from a Supply Chain perspective can bring significant competitive
advantage. As such, TPM is a World Class enabling tool, used to secure:
• |
Business Performance Improvement |
• |
Cultural Change/People Benefits |
• |
Competitive Advantage |
Company-wide TPM recognises that it is customers who
drive our business. We need to provide the necessary responses to not
just satisfy, but also to exceed, the expectations of our customers. The
goal is to maximise added value by eliminating waste in all that we do,
right across the supply/value chain.
TPM is a Continuous Improvement process that strives to maximise equipment
efficiency by creating the perfect relationship between people, their
processes and equipment. It has five founding principles:
• |
Increase the Overall Equipment Effectiveness (OEE) through
focused improvement. |
• |
Make front line Asset Care part of the job. |
• |
Improve existing planned maintenance systems and the
quality of maintenance. |
• |
Increase hand/operational skills and teamworking and problem solving
skills. |
• |
Early Equipment Management: Involve operators and maintainers in
the next generation of equipment design (TPM for Design). |
TPM is both practical and results driven. Applied to
the shop floor, it is a common sense approach that provides visibility
to all the six major losses that are a result of poor equipment performance.
The resultant Business Performance Measure is called the Overall Equipment
Effectiveness (OEE).
The TPM process must be led by manufacturing and encourages production
and maintenance departments to work in harmony as a team, with the goal
of increasing equipment effectiveness and in turn the organisation’s
profitability.
It also involves other departments, such as supply chain administration,
sales and marketing, warehousing and distribution, as well as the more
direct manufacturing support functions of design, quality, production
control, finance and purchasing which are concerned with equipment and
process effectiveness. This of course includes management and supervision.
TPM makes extensive use of waste elimination, standardisation, workplace
organisation, visual management and problem solving.
Like all good “Enabling Tools” TPM must be tailored to suit
the specific organisation and plant.
Adding Value By Eliminating
Waste
The most effective way of adding value is to have a continuous determination
to eliminate waste across the supply chain and thus maximise the Value
Stream: Easy to state, difficult to deliver.
So where do the principles, processes and reality of TPM come into play
to achieve the goal of a “Totally Productive Operation”?
The answer is to view TPM not simply as Total Productive Maintenance in
the sense of Overall Equipment Effectiveness (OEE), Autonomous Maintenance,
5 S’s, Clean Machines and so on, but rather
as the proven roots and origins for applying Company-Wide TPM.
Similarly, “TPM in the Office” is better served by broadening
the application of these sound and proven principles into “TPM in
Administration” embracing all support functions such as sales, marketing,
commercial, planning, finance, personnel, logistics, stores and IT. This
recognises how the whole team contributes to the overall result.
Evolution of a Route
Map to World Class
30 years ago, TPM showed the world that it is a very practical route to
higher levels of equipment effectiveness. Equipment and process problems
are the root cause of many of the unplanned events which reinforce a reactive
management style. Delivering reliable equipment on its own however is
not enough to deliver world class company performance. In helping to tackle
these problems at source, TPM has evolved to address wider management
issues and company-wide TPM has shown itself to be an enabler capable
of delivering overall supply chain effectiveness and hence business efficiency.
What can TPM give
my Business?
The benefits from TPM Implementation are realised under the following
three categories: -
Equipment Benefits |
• |
Improved process capability, reliability, product quality and productivity. |
• |
Economical use of equipment throughout its total service
life starting from design, called TPM for Design or Early Equipment
Management. |
• |
Maximised efficiency of equipment. |
Business Benefits |
• |
Planning with confidence through the Supply Chain to provide what
the customer wants, when they need it, just in time, right first time. |
• |
Flexibility - being able to react quickly to market
changes without high levels of stock. |
• |
Improvement in Overall Equipment Effectiveness (OEE) as a measurable
route to increased profitability. |
People Benefits |
• |
Planning with confidence through the Supply Chain to provide what
the customer wants, when they need it, just in time, right first time. |
• |
Practical and effective example of teamworking including
TPM in Administration for the support functions. |
• |
Trouble free shifts, because value adding activities become proactive
rather than reactive. |
Assessing
the Costs
One of the underlying strengths of TPM is its ability to reduce complexity
and provide the route towards systematic decision making. Experience shows
that a 1% improvement in the OEE is equivalent to between 5% & 20%
of the annual maintenance budget: greater effectiveness leads to greater
savings!
The On-the-Job Reality
TPM Implementation is based on a structured approach as shown in the 3
cycle, 9 step schematic with some fundamental and common sense ideals
as a foundation.
All three cycles of the TPM Improvement Plan involve
the principles of Autonomous Maintenance, as the second founding principle
of Front Line Operator Asset Care.
The audit and review process explained later ensures not only accountability
for this second principle, but also that all five founding principles
are aligned to clear responsibilities of five Pillar Champions.
A key part of TPM addresses cleanliness and workplace organisation - eliminating
dust, dirt and disarray. This is called the 5 S’s
or CANDO. (Cleanliness, Arrangement, Neatness, Discipline and Order).
In summary, TPM recognises that to get a reliable and flawless operation
through Continuous Improvement, it is the people who make the difference.
By unlocking your full productive capacity, TPM unlocks the potential
of your workforce.
How do we get Started?
To introduce TPM principles, philosophy and practicalities into an organisation,
a structured, common sense, step-by-step approach has to be taken. It
is a journey that comprises:
• |
Securing management commitment (typically 3 to 6 months) |
• |
Trialing and proving the TPM route as part of the policy development
(the next 12 to 18 months) |
• |
Deployment of that policy through four milestones (Year 2 onwards) |
Typical timescales will of course vary according to
the size of the operation, the amount of resource committed and the pace
at which change can be initiated and absorbed. All these key questions
plus cost/benefit potential are addressed within the front end Scoping
Study or “Planning the Plan” phase, as the key part of securing
management commitment.
The Potential to
Transform Company Performance
Each year brings new challenges, so that not all decisions can be made
on a computational basis. TPM helps us to control the routine 80%, giving
us the time to focus and innovate around the difficult 20%.
TPM supports such a strategy by delivering:
• |
Organisational activity that reflects future needs of
the changing customer/economic environment. |
• |
An infrastructure to support team-based ways of working (Management
and shop floor). |
• |
Decision processes based on systematic thinking to challenge accepted
practices. |
• |
Team based recognition and rewards systems that align short term
activities with long term business goals. |
• |
A focus on enhancing knowledge rather than defending your corner. |
• |
Improved OEE to enhance supplier customer relationships. |
• |
A mechanism to pull through improvements rather than pushing down
initiatives. |
Most importantly it provides a development route to
enhance the impact and develop the capability of Key Personnel over four
milestones:
These priorities are linked to the future business vision
through the use of a continuous improvement master plan. The master plan
is simply a summary of intentions laid out against the predictable stages
of any change programme.
In order to sustain TPM beyond initial pilot projects
the implementation of TPM has 3 dimensions: -
• |
Top down - target driven management: creating the environment
for continuous improvement (i.e. the BEM Model) |
• |
Bottom up evidence: small group activity |
• |
Resultant organisational learning: capturing and sharing lessons
learnt |
These align with first line and senior management roles
and provide the basis for integrating management priorities. This is also
aimed at giving the bottom up, team-based activity the necessary recognition
at each level of TPM progress.
Alignment and Implementation
At different stages in the journey of using TPM to achieve World Class
Performance, some criteria are more important than others. However, there
are clear links with TPM and the Fundamental Concepts of Excellence which
underpin the BEM:
• |
Results Orientation - TPM is designed to achieve improved
results in a manner that recognises the needs of the main stakeholders. |
• |
Customer Focus - TPM will lead to improved product quality and responsiveness. |
• |
Leadership and Constancy of Purpose - TPM allows leaders to reinforce
the culture of excellence. |
• |
Management by Processes and Facts - TPM demands that the organisation
is knowledgeable about the productive effectiveness of its assets,
and is measuring, targeting and improving their performance towards
world class standards. |
• |
People Development and Involvement - TPM requires that employees
are skilled in their discipline, that they are encouraged to become
involved in ongoing improvement activities and recognised for it. |
• |
Continuous Learning, Innovation and Improvement - TPM creates a
clear picture of the organisation’s productive potential. This
helps to establish a clearer picture as to when incremental improvements
must give way to re-engineering and thereby stimulate innovative thinking
at the appropriate time. |
• |
Partnership Development - with a considerable reliance on third
parties for production equipment and resources TPM provides a useful
platform on which to base joint improvement activities. |
• |
Public Responsibility - the TPM focus on Health and Safety and Environmental
responsibility directly support this concept. |
The necessary alignment is provided by bottom-up evidence
of the quality and status of the TPM journey through the four milestones,
by very precise and exacting eight levels of Audit. The diagram below
shows the audit and review criteria for the Level 1 Checklist and how
it provides recognition at each level as the evidence of success during
the Roll Out of TPM though geographic improvement zones in the plant.
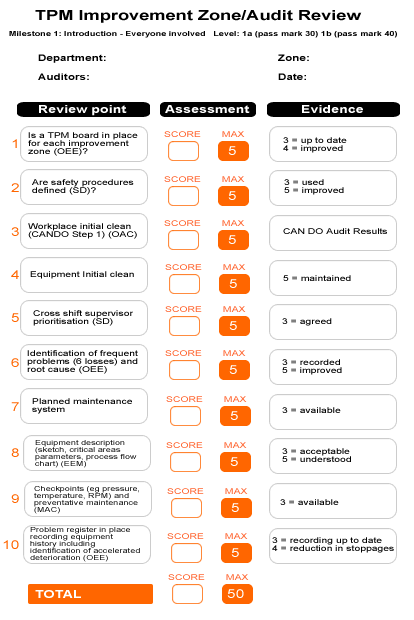 |
• |
Against each of the ten review points there is a nominated
pillar champion with responsibility for each of the five founding
TPM principles: Review points 1, 6 & 10 is the OEE Pillar Champion,
2 & 5 the Skill Development Champion, 3 & 4 the Operator Asset
Care Champion, 7 & 9 the Maintainer and Quality of Maintenance
Champion, and finally review point 8, the Early Equipment Management
Champion. |
• |
For each review point there are detailed standards set against which
to benchmark the assessment score. As well as the total score achievement
each review point must achieve at least 3 for level 1A and at least
4 for level 1B. |
Conclusions
Together, the BEM and TPM have important complimentary roles. The BEM
can at a high level, help identify and reinforce the priority for improving
Total Productive Manufacturing. It also helps to understand all the component
activities and people who contribute to successful TPM. Having established
the need for improvement, the TPM disciplines can be applied to provide
the necessary and important next level of detail, as well as the practical
frameworks for delivering improvement.
When used together, BEM and TPM provide a powerful force for building
and sustaining true competitive advantage.
top of page |
 |